What are the Most Common OSHA Violations and How Can Employers Keep them from Happening in the Workplace?
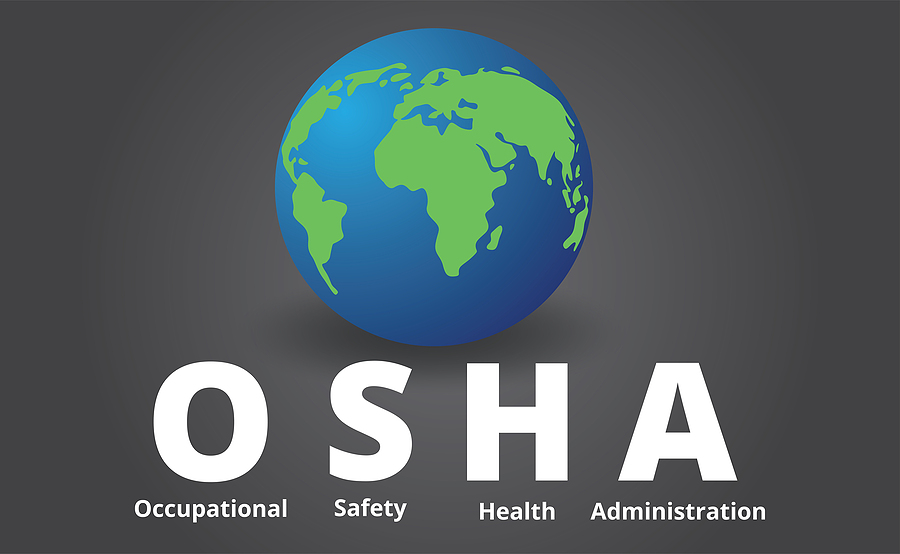
During and after industrialization, employers hired more workforce to match market demand. Unfortunately though, there were no safety guidelines for workers at that point.
In the US, there was no state department in the USA to monitor these occurrences, which resulted in employer negligence resulting in injuries and deaths until 1970. The government authorized the creation of the Occupational Safety and Health Administration (OSHA) in 1970.
The main objective of this organization is to make sure that safety practices are followed at workplaces, the workers are aware of their rights and are protected while on site.
What does OSHA Violations mean?
Safety on the work site should be a top priority for any employer. Due to that, there are updates from OSHA on a periodic basis which issues a list of standards to be followed at worksite. These standards must be applied by all companies and employers.
However, certain companies did not adhere to these standards and do violate OSHA regulations. In a worst-case scenario, these OSHA violations lead to a hefty fine or a shutdown of the working site.
List of Common OSHA Violations
Each year, OSHA releases a updated list of these OSHA violations on their website. These violations are mostly petty and are often committed at the working site because of ignorance.
Most violations are not serious, and OSHA can fine or bar contractors from working. Below we will discuss common OSHA violations and how to avoid them.
Fall Prevention
Workers are required to work at elevated working sites most of the time. The risk azards of slip and fall from higher working sites are greater than ground sites.
In USA alone, there over 300000 are injured, and more than 300 are killed due to falling from the height every year. Slips, trips and falls from heights remain a constant danger, and firms must adhere to OSHA safety guidelines.
Safety Precautions
- Maintain the work areas free of water, debris and waste
- Ensure the worksite has strong illumination lights.
- Danger signs are responsible for separating workers from dangerous worksites.
- Provide OSHA-recommended footwear to workers.
- Periodically check the condition of scaffolds or ladders.
- Add side railings and hooks on the raised paths for assistance.
Identifying Hazards and Communicating Them to Workers
Materials and chemicals used on the work site are a major threat to the safety of workers.
If they understand what chemicals and materials are in play, then they can take measures to protect themselves. This can be done with the OSHA Hazard Communication plan. This plan involves four sections:
- Descriptions of the safety program in written form.
- Extensive warning labels and signs.
- Material safety datasheets
- Workers training coaching sessions
Protection of the Respiratory Airways
When an individual works in the worksite, he or she is exposed to dust particles, metal scraps, poisonous gases and chemical fumes to be inhaled.
Long-term exposure to these elements can cause serious lungs diseases. An employer or contractor shall furnish his workers with OSHA approved masks or respirators. These respirators have an air filter that filters out and prevents the dust particles and gas fumes from reaching the lungs.
Make sure that mask covers mouth and fits tightly.
Individuals with large beards may have difficulty using respirators. Therefore, they must cut the beard according to the adjustment of my respirator.
Scaffolding
Scaffolding is the equipment that workers need in order to build, clean and repair at a height. Well according to OSHA, weak or substandard scaffoldings are the leading cause of casualties at the worksite. OSHA has provided the following guidelines for the safe use of scaffoldings:
- In scaffoldings more than 10 feet high, use guardrails.
- Daily inspection of the scaffold guarding, scaffold plank or the deck that we make underneath the scaffolding.
- Side ladders or hooks should be installed to allow workers to safely get on and off the scaffoldings.
- Keep the distance between the planks or decks the same
- Make sure you put the scaffold on a firm and even surface to avoid stumbling.
- Providing employees with information on scaffold usage and purpose can help limit injuries.
Ladder
Ladder is also an essential equipment as it helps get to the top of the site. At the worksite, depending on the need, ladders of various sizes and made of different materials are used. Some of OSHA’s guidelines regarding the use of ladders include:
- Ensure that the steps of the ladder are not loose, wet or slippery.
- The A-frame ladder must rest on stable ground.
- Regular inspection of side locks integrity while the ladder is open.
Lockout/Tagout (LOTO) Protocol to Control Hazardous Energy
Hazardous energy is the term used to describe the waste material or debris exudate by the machines employed in the worksite. These materials when released in the form of debris or scraps can hurt the workers. The best way to avoid this OSHA violation is to follow the LOTO protocol. LOTO protocol guidelines are like:
- Inform the employees of the specifics of the LOTO process.
- Through regular auditing of the machines in operation.
- They need a special observation and monitoring for new machinery.
- Always buy and use mechanical tools approved by OSHA.
Forklifts and powered industrial trucks
The on-site incidents that result due to the use of powered industrial trucks or forklifts are enlisting amongst the top 10 OSHA violations USA. Forklifts are widely used in various industries, hence competent personnel must be trained to operate them. OSHA has come up with exhaustive guidelines regarding use, selection, driver criteria etc of a forklift and non-compliance with these guidelines attracts huge penalties by OSHA. Here are the guidelines regarding the use of forklifts at the worksite:
- Training sessions should educate all workers about forklift use.
- Create a perimeter for where forklift can or cannot enter
- Your forklift operator should always be a licensed worker.
Protection of Eye and Face
Many work calls for the immediate contact of workers with materials that are hazardous, chemical or radical. Hence, eye and face protection gear becomes mandatory for the employees working in these worksites. Here is complete OSHA guidelines an employer must follow to keep the workers safe:
- Sufficient traing on potential dangers and material dealing.
- Eyewash stations at the worksite to use in an emergency
- Inform workers on First Help methods.
Fall Protection Training Program
The high building work is a risky business one, and the workers of these companies are more likely to slip and fall from the scaffolds. OSHA guidelines such companies develop a comprehensive fall protection training program for their employees.
If found guilty of failing to do this, it is treated very harshly and regarded as an OSHA violation. To prevent this breach, corporations must obey the following tips:
Every employee should master the four-level of this program, which includes. 1) completely aware of potential hazards, 2) authorized user, 3) competent personnel, 4) qualify for the fall training program.
Companies must record and maintain the skill and training of each employee.
Machinery Protection
Also all the machines which are being used at the worksite should be properly guarded. Scrap and sparks flying and moving parts of the machine can seriously injure any worker. In order to prevent this type of OSHA violation:
Conduct training for the employees to make them aware of machinery protection significance.
Perform regular checks on the machine guards in use and replace the old ones.
OSHA guidelines are meant to protect workers from harm in the workplace. The chances of his compliance with them reduce the chances of injuries and causalities to the least possible limit. By correcting these mistakes, there is no OSHA violation and therefore no penalty or fine. A healthy environment leads to a healthier worker and improved efficiency.