Top Steps Needed To Enhance Your New Mexico Workplace Fall Protection Training
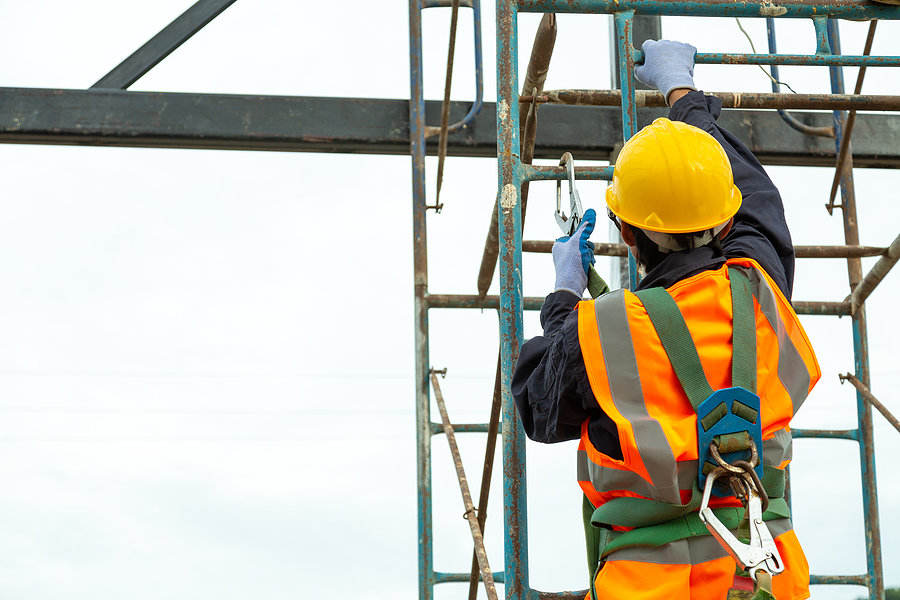
According to OSHA, falls from height are a leading cause of workplace injuries and fatalities and were the most frequently cited OSHA standard in 2021. By undergoing proper and effective fall protection training, you can be assured that your employees are equipped with the knowledge to operate safely and help prevent these incidents.
Fall protection training is not just an exercise in ticking the box. There’s nothing more quintessential to an effective fall protection program than the appropriate training to live alongside it.
You can use these fall protection training steps to educate workers on operating safely at your Albuquerque or New Mexico construction company and to improve your current fall protection training.
Always Start with The Basics
It doesn’t matter if your workers are using fall protection for the very first time, or they’re seasoned veterans, they need to be taught – or reminded – of the fundamentals of how to keep themselves safe.
Rubin suggests that starting with topics such as harness sizing and fitting will help workers to recognize that proper fit of equipment is critical.
Going back to the basics is beneficial no matter how much experience a worker may have. For example, if a harness doesn’t fit properly, it won’t be hitting you at the right spots and you aren’t fully protected in the event of a fall.
The next step would be to teach workers about other equipment – such as lanyards, lanyard extensions and scaffolding – that are designed to help them keep safe. This training ensures that even the novice will feel confident with the equipment they are using.
As a good employer, providing equipment is the first step, but totally useless if your workers don’t know how to use it in different environments. Get you workers to practice using the equipment so that when they come to using it in the field, it becomes second nature, and they will be confident that they’ve made the right decision.
Simulate The Work Environment
Of course, theory is all very well, but proper training includes simulating the environments that your workers are likely to be faced with. Simulating those environments is a key part of training so that your workers can visualize and apply their knowledge in every situation they may encounter.
By simulating potential environments, you also give your workers a safe place to make mistakes. A fall protection simulator will allow your employees to run through different components using different fall protection equipment that may be required for a specific project.
For example, a simulator that trains workers operating on scaffolding to perform their tasks and traverse a scaffold while remaining tied off the entire time enables the worker to recognize potential consequences if something goes wrong, and to make the right decisions.
Conversely, learning what not to do is just as important as learning what to do. An environment that’s live and experiential that allows mistakes to be made will enhance confidence about making the right decisions out in the field.
Practice, Practice, And More Practice
Once you’re confident that you’ve taught workers to use their equipment and have put them through a simulated work environment, they need to practice using that equipment in those environments. By ensuring their confidence in the simulated work environments, it’s far more likely that they will repeat their actions in a real scenario.
You practice like you play and with fall protection, we’re playing for keeps. Training is especially crucial because it can mean the difference between life and death.
However, training should not be a one-and-done experience. With the advent of changing working conditions, workers should receive regular refresher courses throughout the duration of the project.
Repetition is the key. Employees should not be getting into a harness on the job until they’ve had suitable training. It should be part of their initial orientation and refreshed around every 3 months throughout the duration of the project.