The Bottom-Line Regarding OSHA Workplace Injury Reporting and Recordkeeping
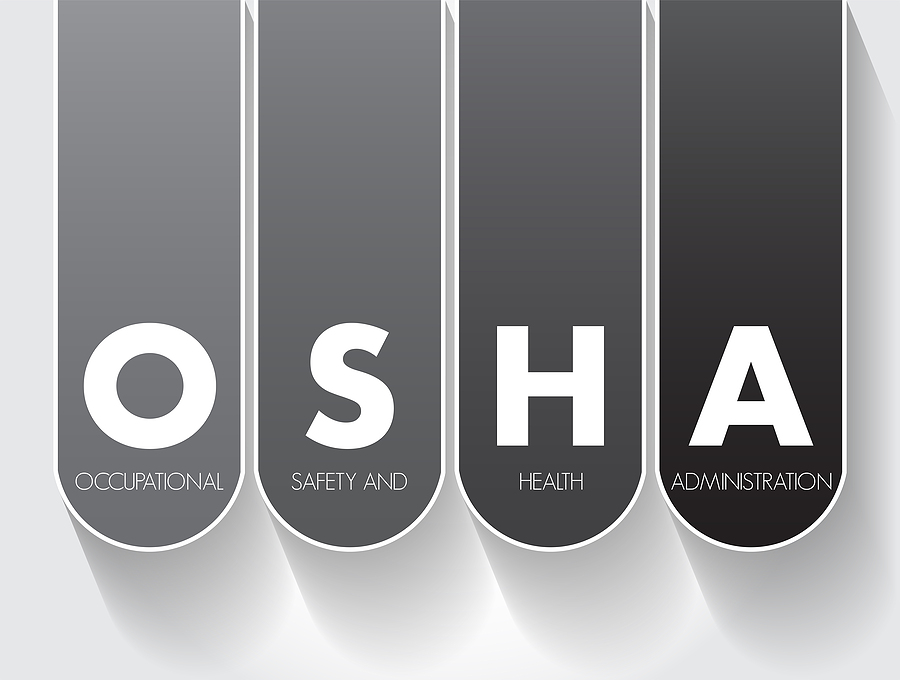
When an accident or injury occurs on the job, the first thing that often goes through anyone’s head is not, “we need to report this to the Occupational Health and Safety Administration.” Instead, the first thing that should be done is to get medical assistance, and then you should focus on figuring out how to fix the problem that caused the occurrence. After that follows an analysis of the economic repercussions, which include worker’s compensation, lost productivity, and future legal claims, among other things. The OSHA reporting and recordkeeping procedure, even though it might not appear as urgent as a worker who has passed out or as a forklift that has fallen over, is an essential aspect of environmental health and safety management. And because the minimum penalty for a single missed or late report is $5,000, an occurrence that needs to be recorded and reported promptly might bring significant expenditures to many companies. The Importance of Keeping Accurate OSHA Records. Recordkeeping and report filing should be highly prioritized for various reasons, not the least of which is the desire to avoid incurring regulatory fines. Take into consideration the following advantages outlined by OSHA:
Keeping a record of accidents and injuries on the job can help enhance injury prevention.
Records may reveal patterns and commonalities among the problems troubling an institution. However, the purpose of any environmental, health and safety (EHS) program should be to safeguard the workforce proactively (rather than only reacting to occurrences), and this can be accomplished only if you can predict what is likely to occur.
Utilizing data on injuries sustained on the job helps identify issue areas and procedures that may be used to improve unsafe working conditions.
You can better recognize potential dangers and reduce their impact when you have more information. If you take it a step further and evaluate the data, you will be able to establish where your safety program is lacking and where there are holes. For example, you could discover that personnel want further training or that a particular method is rife with opportunities for mistakes.
Improve the way the organization manages its health and safety initiatives.
Again, having well-recorded data is the most reliable approach to evaluate the effectiveness of your program. You may determine whether you are actually and demonstrably bettering your safety outcomes by analyzing your data. When workers’ understanding of safety issues increases, they are more likely to adopt safe practices and report risks they encounter. The maintenance of records and the promotion of a secure working environment form a virtuous cycle. The more you learn, the more conscious you’ll be of the facility and its essential areas, such as training or personal protection equipment, as you increase your level of expertise. Employees have no excuse to protect themselves and keep an eye on the conduct of their coworkers when it is made clear to them that the usage of personal protective equipment (PPE) demonstrably links to enhanced workplace safety, for example.
Exceptions made for employers under the OSHA Recordkeeping Requirements
Keeping detailed records may be optional for some businesses, even though doing so is virtually universally recommended. OSHA exempts most of its recordkeeping requirements for companies with less than 250 employees. You are exempt from the need to keep safety records if you never have more than ten employees at any given time during the year. If you do not choose to do so, you do not need to fill out OSHA forms 300, 301, or 300A.
Businesses operating in fields with minimal risk of injury are eligible for some exemptions. Even if you work in what OSHA considers a “low-hazard business,” your company is still obligated to comply with the reporting claims standard; however, you are exempt from the need to keep OSHA 300 records (although doing so remains a best practice). You will need to find your North American Industry Classification System (NAICS) code to determine whether your place of employment is considered to have a low risk of injury. After this information, you can check the OSHA website to see if your NAICS code is included on the list of partially exempt industries. Please keep in mind that we are discussing exemptions that are just partial. You are still responsible if OSHA or any other agency demands that you preserve these forms; for instance, if the Bureau of Labor Statistics conducts a random sample and requires you to maintain records throughout the year, you will be held accountable.
Whether or not they are exempt, all companies must record fatalities and serious injuries that occurred on the job. In addition, if you keep OSHA logs, you need to ensure that your records are kept for at least five years. To return to the inquiry raised in the heading of this article: Do you truly need to ensure that you comply with the recordkeeping rules set out by OSHA? The answer is unequivocal “yes” for many different types of businesses. Regarding the other questions, the answer is “yes, you probably should.” Recordkeeping is the best management practice that should be followed by every business, regardless of whether that organization is exempt. In addition, keeping records might assist you in controlling the expenses of workers’ compensation claims.
Contact Safety Counselling at the following number: 505-881-1112 to obtain further information and directions concerning OSHA recordkeeping and reporting.