How Personal Fall Arrest Systems Save Lives at Construction Work Sites
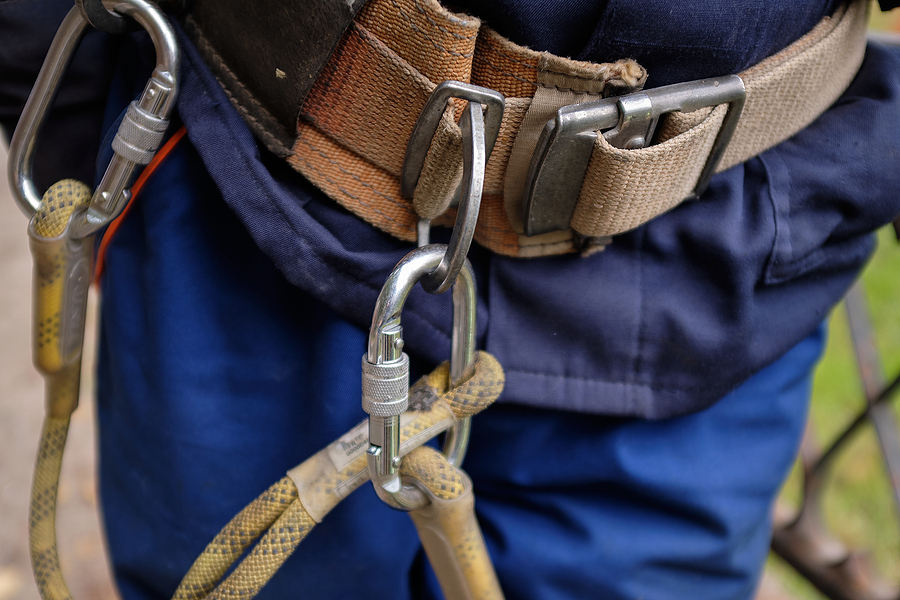
OSHA has identified that fall hazards are among the biggest causes behind fatalities that take place within the construction industry. This is why you should pay special attention to Personal Fall Arrest Systems. The current fall protection systems people use at job sites are mostly not capable enough to reduce the number of fatalities happening.
What is a Personal Fall Arrest System (PFAS)? I tis capable of safely stopping or arresting a worker who falls from a working level. It is equipped with a connector, anchor point, and a body harness. The following requirements must be met by the personal fall arrest system (PFAS) when it is selected as the fall protection method on a working site
- Set a maximum arresting force to 1,800 pounds for construction worker used with a body harness.
- Be constructed in such a way that a worker cannot fall more than 6 feet or make touch with any lower level.
- Bring a worker to a full stop and restrict their ability to accelerate more than 3.5 feet.
- Be strong enough to resist the impact energy generated by a worker free falling six feet, or the maximum free fall distance allowed by the system, whichever is less.
- Be checked for wear, damage, and other degradation before each usage. It is necessary to take defective components out of service.
- OSHA Standard 1926.502(d)(16)(iii) Employee’s must have a personal fall arrest device set to stop falls at no higher than 6 feet.
- A worker on an aerial lift using a personal fall arrest device, a safety vest, and a hard helmet.
Employees must get thorough instruction on how to choose and use personal fall arrest devices. The device can cause severe harm or death if it is used carelessly or improperly. Workers must receive training in the safe use of the system. The training should cover
- Detailed instructions on how to properly put on harnesses
- The limitations of the fall protection equipment
- the right techniques for anchoring and tying off, and estimation of the free fall distance, including calculating the deceleration distance, in order to prevent hitting a lower level.
- The best system to use will depend on its techniques of usage and the particular circumstances present at the jobsite.
- Storage system inspections
Standard 1926.503(a)(1) of OSHA ensures that for each person who could be exposed to fall dangers, the employer must provide a training programme. The programme will make it possible for each employee to recognise the risks associated with falling and will teach them the steps to take in order to reduce these risks.
Before each usage, the user must check the personal fall arrest system equipment and retain a written record of the examination. Be on the lookout for worn, damaged, or flawed parts while conducting a PFAS check.
Do not use the device if there is any question as to its safety. Before using the system, replace any damaged equipment. Ropes and other equipment that have been a part of a fall should be taken out of operation.
Standard 1926.502(d)(21) of OSHA Personal fall arrest systems must be checked for wear, corrosion, and other degradation before each usage, and any faulty parts must be taken out of service.
Any component having a serious flaw must be promptly taken out of service, labelled, or declared as useless, or destroyed. Look out for the following during the PFAS inspection:
- Cuts, rips, abrasions, mould, or excessive stretching
- Any additions or modifications that can reduce its effectiveness.
- Contact with fire, acids, or other corrosives
- Harm from degradation.
- Misaligned or defective hook springs
- Tongues that don’t fit snugly against buckle shoulders.
- Missing or broken mountings
- Faulty components
One of the most crucial components of fall arrest systems is thorough planning, which involves thinking forward to a proper anchor point. A competent individual should assess the anchor points before usage with an emphasis on adequate strength. The following are some examples of anchor points:
- Steel members or l-beams (They need to be used if a suitable strap is available to make a connection)
- Large eye-bolts manufactured of a suitable grade of steel.
- Guardrails or railings that have been made to serve as anchor points
- Other properly planned anchorages developed by a professional engineer or competent person
- Wood members or masonry provided the attachment point is significant and care have been taken to ensure that bolts or other connections will not pull through.
- Other types of anchorage that a qualified person such as a professional engineer design.
A personal fall arrest device can link to a lifeline rather than directly to a fixed anchor point. A lifeline is an appropriate anchor point-connected vertical, horizontal cable or rope.
A worker can climb a vertical lifeline using a rope grab (also known as a cable grab), and if the worker falls, the rope grab will automatically engage and lock on the lifeline. The rope grasp must be appropriate for the lifeline and properly fastened (not upside down). Rope grabs should be placed as high up on the lifeline as practicable and the lanyard between them should be as short as possible. Each employee has to be secured to their own vertical lifeline.
Full-body harnesses are available in a range of designs to accommodate various working environments. Depending on whether a harness will be used mainly for positioning, climbing, limited places, or a mix of labour duties, it can be constructed significantly differently.
A D-ring on the rear of a full-body harness is necessary for securing a lifeline or lanyard. The D-ring’s location eases physical strain and maintains the wearer’s upright posture in the harness during and after a fall. For positioning, scaling ladders, and lifting or lowering employees into small places, certain safety harnesses incorporate extra D-rings on the shoulders, hips, or chest.
A seat sling, belt, belly pad connector, high-visibility garment, or other accessory can be compatible with a harness.
Use only industrial full-body harnesses, not climbing leisure harnesses, for work.
To maintain and clean the parts of the fall arrest system, including the body harness, follow the manufacturer’s recommendations. After cleaning a PFAS, avoid letting the equipment sit in the sun for an extended period of time and keep it away from sources of intense heat. Equipment containing PFAS should be stored in a place that is clean, dry, and devoid of fumes, sunlight, corrosive substances, sharp edges, and vibration.
A lanyard is a specifically made flexible rope with snap hooks normally attached at either end. The body harness is attached to one snap hook, while an anchor point or lifeline is attached to the other. A minimum breaking strength of 5,000 pounds is required for lanyards.
Lanyards are available in many different designs, such as self-retracting models that facilitate movement and shock-absorbing models with single or double legs. Never tie lanyards together to shorten them or combine them to lengthen them.
Standard 1926.502(d)(9) of OSHA – A minimum break strength is required for all lanyards and verticial lifelines.
The PFAS’s necessary deceleration devices, which include rope grips, self-retracting lifelines, and shock-absorbing lanyards, protect employees from the force of a fall. If the shock absorber is even halfway stretched or if the lanyard has stopped a fall, never use it. In order to prevent disengagement from any component portion of the personal fall arrest system, snap hooks must be of the locking kind.