Forklift Safety Training – Top Methods from Certified Forklift Safety Training Programs
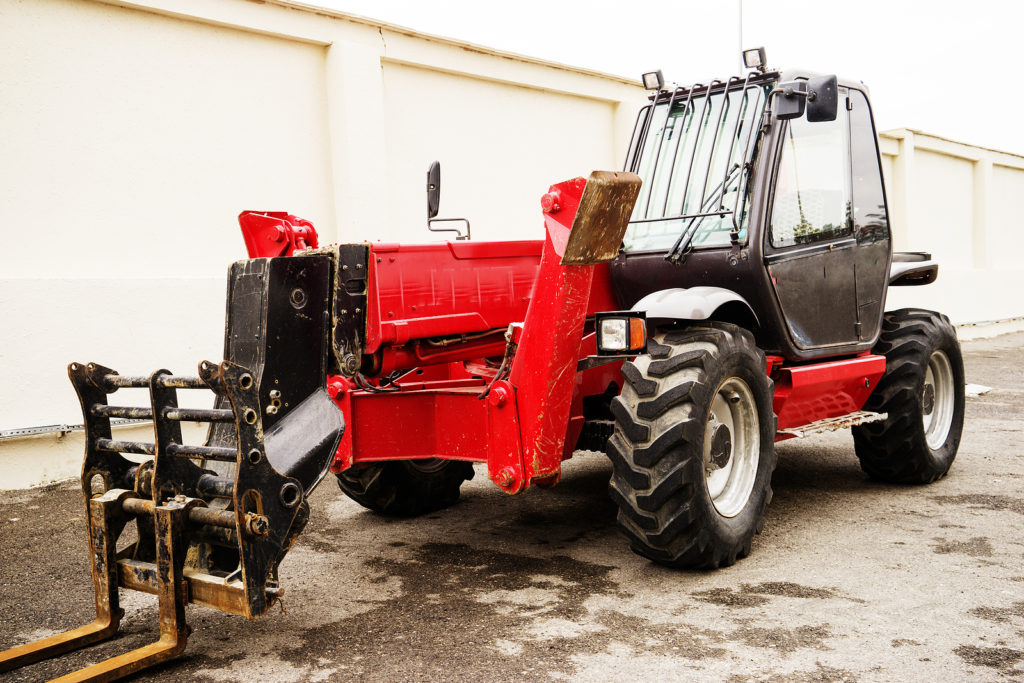
In many warehouses, factories, construction sites, and other working areas, a forklift is an essential piece of equipment. It enables workers to lift, stack as well as transport heavy loads and materials that are beyond human strength to handle. Even so, these machines, which are so strong, can also be very dangerous if they are not handled with care and precaution.
OSHA estimates that close to one hundred Americans die every year due to forklift accidents, with tens of thousands more being injured seriously. Many such incidents may be avoided through a comprehensive training program for operators of forklift trucks.
In this article, we will discuss certified courses on the safety precautions taken regarding forklifts. This will enable us to understand why training is highly emphasized because we shall look at what causes most of the accidents occurring during forklifting exercises.
Examining Common Causes of Forklift Hazards
Forklifts may seem straightforward to operate, but they can easily turn dangerous in many different ways if operators are not trained. Some of the most frequent causes of forklift accidents and injuries include:
Speeding Aggressively
Driving forklifts at excessively high speeds is an enormous hazard that greatly reduces the operator’s reaction time and vehicle control. Even small bumps in the road or slight turns can cause catastrophic tip-overs or dropped loads when the driver is moving too fast to respond safely.
Forklift operators must always maintain cautious, defensive driving speeds appropriate for the specific conditions, load weight, and environment. Speeding aggressively on a forklift has caused countless avoidable deaths when the vehicle tipped over on top of the operator or struck workers moving too fast to stop.
Lack of Communication
Insufficient communication between forklift drivers and nearby workers or pedestrians is a primary cause of painful, traumatic collisions that can permanently disable or kill. Constant vocal communication, warnings, and signals are essential to ensure all people in the vicinity are fully aware of the forklift’s presence, directional movements, and intended path.
Drivers should utilize horns liberally so no one can claim they were unaware of the approaching forklift. Clear communication eliminates collisions.
Missing Audible Warning Systems
Warning lights, horns, and backup alarms installed on forklifts serve critical safety purposes by loudly alerting nearby workers and pedestrians that the heavy machinery is in motion nearby so they are not accidentally struck.
Missing, damaged, or deactivated audible warning systems on forklifts drastically increase the risks of collision, especially in loud warehouses that muffle movement sounds. Workers can easily wander into the vehicle’s path unknowingly without blaring alarms.
Utilizing Incorrect Driving Techniques
Failing to follow proper defensive driving procedures for turning, parking, loading, unloading, reversing, driving on inclines, or other basic techniques leads to many deadly forklift accidents every year.
Unlike driving a car, safe forklift operation requires specialized skills that must become ingrained muscle memory through hands-on practice under close supervision. Attempting improper procedures like fast turns or parking on inclines can easily tip over the forklift.
Inadequate Maintenance Checks
If forklift operators cannot properly inspect their vehicles before shifts, recognize subtle signs of mechanical issues, or immediately report damages or problems, poorly maintained forklifts put everyone at grave risk due to unpredictable breakdowns, tire blowouts, or other malfunctions while loaded or in motion. Daily preventative maintenance checks and reporting issues early is absolutely vital to avoid potentially disastrous failures.
Unstable Loads at Height
Carrying extremely high, off-centered loads when moving at high speeds can shift the vehicle’s center of gravity and easily cause catastrophic tip-overs. Even at slow speeds, highly elevated loads make the forklift incredibly unstable and prone to flipping over sideways if the operator makes any sudden turns or hits bumps. Loads must only be lifted substantially when the forklift is fully stopped and balanced.
Why Forklift Training Programs Are Absolutely Vital
There are several compelling reasons why comprehensive forklift training incorporating both classroom education and hands-on practice should be considered mandatory at any organization that uses this equipment:
Preventing Loss of Life
Given their massive size and heavy loads, forklift accidents can easily turn deadly in the blink of an eye. However, proper training in defensive driving principles can mean the difference between life and death.
Catching Mechanical Problems Early
Classroom training allows operators to fully understand their equipment and quickly recognize subtle signs of mechanical issues before they lead to breakdowns or malfunctions. Catching problems early is critical.
Building Safe Driving Habits
Both lectures and hands-on practice reinforce vital safe driving techniques for load management, maintaining visibility, cautious acceleration and braking, and much more. This drastically reduces accidents.
Avoiding Costly Downtime and Repairs
Accidents due to untrained operators can lead to extremely expensive downtime, halted production lines, damaged products and inventory, and high repair costs. Proper training avoids these expenses.
Improving Operator Confidence and Morale
Formal training gives operators confidence in their abilities and assurance that all coworkers have been held to the same safety standards. This improves comfort, morale, and productivity.
Key Training Techniques Used by Certified Programs
High-quality accredited forklift training programs utilize a multifaceted approach to instill safety consisting of classroom lectures, demonstrations, hands-on driving practice, evaluations, and refresher courses:
- Classroom Presentations: Classroom sessions present foundational concepts through presentations, videos, materials, and lectures on equipment operation, inspections, load handling, and workplace rules.
- Practical Demonstrations: Instructors first demonstrate proper pre-operation inspections, safe driving techniques, load handling, and more so trainees fully understand proper procedures before attempting them.
- Extensive Hands-On Driving: Under close supervision, trainees get extensive real-world practice driving the forklift, controlling loads, parking, reversing directions, and inspecting the vehicle to build skills.
- Realistic Workplace Simulation: Exercises mimic real-world hazards and environments to practice driving around obstacles, handling uneven loads, communicating with pedestrians, and more.
- Written and Performance Testing: Operators must pass written knowledge tests and performance evaluations on their driving abilities at multiple stages before earning their certification.
- Continuing Refresher Courses: To keep skills sharp, accredited programs require short refresher courses periodically on updated equipment, procedures, and workplace rules.
Conclusion
These forklift programs are very effective in avoiding tragic injuries among their operators through the comprehensive use of a mix of classroom and hands-on training approaches.
However, there is a cost to this training process but it is worth spending since employees’ safety will be guaranteed and enormously costly accidents will be avoided. In any workplace that employs forklifts, getting trained by properly qualified staff can make all the difference between having proficient operators or accidents waiting to happen. The profit margin also benefits from keeping workers safe through such enlightenment.