Critical Facts to Know about Top Fall Protection Training
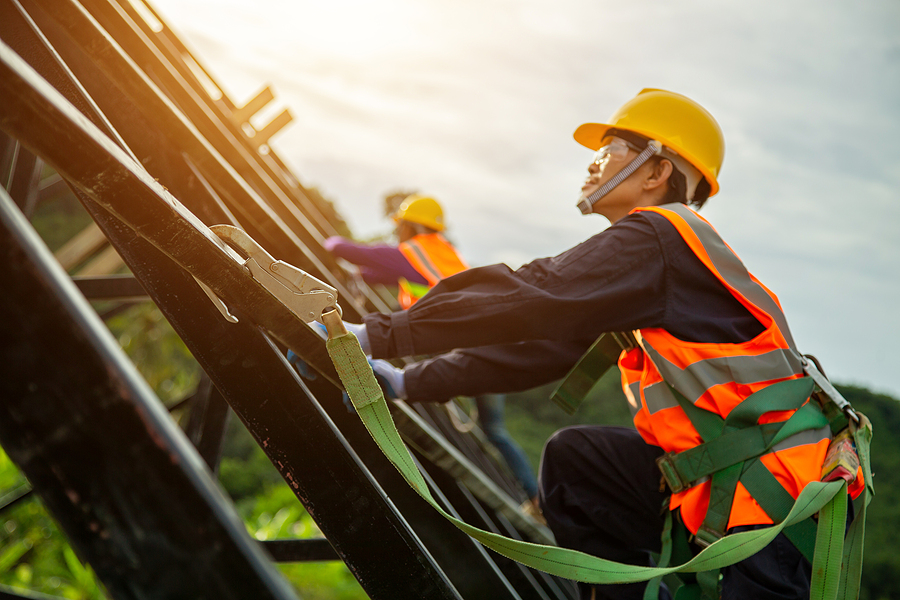
This is vital information to know. After transportation, falls are the second most prevalent cause of workplace fatalities. Employers must give proper Training for workplace falls, which many don’t do. Therefore, OSHA has made it a rule for them too. There are many factors to consider when creating a workplace fall training program but determining the dangers and obtaining the appropriate Training is crucial.
Evaluating and selecting the correct trainer is also critical.
Workplace falls, including slip and trip risks, cause many injuries and deaths. Obliging employers to develop fall protection training program is now OSHA’s law.
How do you stay compliant?
Slips, trips, and falls are among the deadliest workplace dangers your employees face. After transportation, falls are the second most prevalent cause of workplace fatalities. Examine the five-year pattern of falls:
According to the Bureau of Labor Statistics’ “Census of Fatal Occupational Injuries Summary, 2016,” fatal work injuries from falls, slips, or trips increased by 6% to 849 in 2016 and 25% since 2011. Fall Protection – General Requirements (1926.501) and Fall Protection – Training Requirements (1926.501) are the most frequently cited workplace safety violations in this year’s OSHA Top 10. (1926.503). General Requirements had 6,887 citations, and Training Requirements had 1,724.
Workplace falls have always been a severe concern for employees. OSHA has tried to reduce the risk by requiring a separate violation of the fall protection training.
According to EHS Today, OSHA requires organizations to identify slip and fall hazards and provide proper Training to personnel who may be exposed to those hazards (29 CFR 1910.30(a) (1)).
What Do Workplace Falls Cost Companies?
Slips, stumbles, and falls cost businesses money. Recent research shows that falls accounted for $16.1 billion in overall injury costs in 2014.
With OSHA’s latest regulation, it’s no surprise that many citations include training requirements for workplace falls. Creating a thorough training program helps save lives and decrease injuries, not merely avoid costly penalties and legal implications.
Here are five key factors that safety and business managers should know before starting a fall prevention training program.
- What Type of Fall Protection Training Do You Need?
Just as no two businesses create the same product, no two workplaces have the same dangers. The four stages of Training are awareness, authorized-user, competent person, and qualified person.
Because personnel aren’t working with the equipment, awareness training lacks a hands-on component. On the other hand, Authorized-user Training is more extensive, with staff subjected to job-specific Training. Typically, a supervisor or manager is liable for other employees abusing equipment or being exposed to potentially hazardous situations. Finally, qualified-person Training allows people to deal with specific problems and make their safety plans.
Your shop may require a part, if not all, of this Training.
- Ahead of Time: Identify and Eliminate Fall and Trip Hazards.
Beyond selecting who requires Training, you’ll need to decide what they’ll be instructed on and whether any possible dangers can be addressed in the meantime.
Engineers can assist in discovering known dangers before depending on adjustments once an employee has recognized a threat. A) clearly define the hazard, and B) incorporate it (along with other hazards) into the core of your training program.
Regard surface transitions and lighting (color, contrasts, shadows, and intensity) to ensure they are acceptable for the setting. There are several ways to reduce the danger of a fall.
Select the Right PPE: Fall Protection
Do you need assistance in determining the most appropriate personal protective equipment (PPE) for your unique fall protection situation? We have a wide range of Personal Protective Equipment (PPE), including anchoring connectors, fall protection kits, harnesses and belts, lanyards, fall limiters, and horizontal and vertical systems.
When it comes to matting, whether it’s anti-fatigue or entry matting, our interactive selection makes it easy to find the products you need to make your workplace safe.
- Choose the Proper Fall Protection Trainer and Fall Training Program
As soon as you’ve determined the fall dangers present in your workplace and the categories of employees that require Training, you’ll need to pick the most appropriate instructor, depending on your state or location. The National Safety Council provides on-site and online fall prevention training programmes, but word-of-mouth is likely to be your best choice for locating the right training programme for your needs.
Make every effort to maximize the efficacy of the lessons. Generally speaking, hands-on courses held on-site with a low student-to-instructor ratio are preferable.
- Keep a record of all of your slips, trips, and falls!
Although proactive, preventative training programmes are essential in keeping your employees safe from workplace falls, they also ensure that the past does not repeat itself in the future.
According to OSHA, employers with more than ten employees are already required to maintain a record of major work-related injuries and illnesses. It is a proven approach to urge businesses to pay closer attention to harmful activities and rapidly develop ways to fix them if they keep complete and precise records of everything they do. Record-keeping is also an excellent way to protect your own company and brand, which is especially important when courts want you to detail an individual’s type of Training before a traumatic event.
Workers contribute to the financial success of enterprises, but they must be protected from harm. Safety experts are in charge of protecting workers, ensuring that production doesn’t slow down and that disability is kept to a minimum so that people don’t get hurt.
- Finalize the frequency of fall protection training
Workers are considered “trained” by the Occupational Safety and Health Administration (OSHA) after finishing an initial training program. However, the ANSI/ASSE Z359 standard suggests that employees be trained every two years—mainly where the Training is related to workplace falls. However, while the frequency of Training for your employees is totally up to your discretion, erring on the side of caution—and providing ongoing safety instruction for your employees—is almost certainly the most prudent course of action. After all, they are your most valuable resource.
Workers contribute to the financial success of enterprises, but they must be protected from harm. Safety experts are in charge of protecting workers and making sure that production doesn’t stop and that disability costs don’t go up. Top fall protection training is vital to the safety and success of your company.