What are the Top Forklift Safety Pitfalls to Avoid?
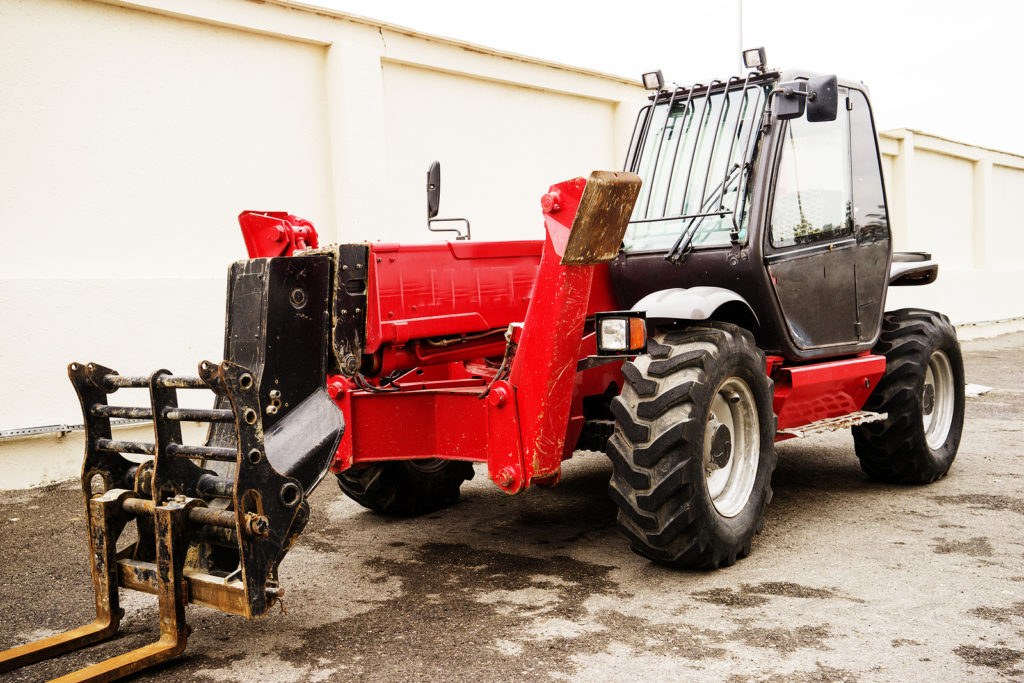
The Occupational Safety and Health Administration (OSHA) reported that almost 100,000 people are injured due to forklifts annually. There are numerous potential dangers associated with operating heavy machinery.
Accordingly, OSHA mandates certification and training for drivers who operate such machines. While a forklift safety checklist can help you and your team, accidents can still happen.
Below are some of the most common safety issues and how to avoid them:
Not Conducting Operator Training
Preventing injuries and fatalities starts with appropriate training for your team. OSHA’s standard for powered industrial trucks mandates that each employee receives formal instruction, practical training, and evaluation in the workplace. Employers must also train and evaluate the skills of each operator, depending on the equipment and work environment, even if a new worker has experience.
Forklifts are different, which is why training also might be different.
It is equally important to be re-trained once in every three years. it reinforces safety fundamentals with operators. And it keeps them in the loop on safety updates.
Failure To Conduct Recorded Pre-Operation Checks Prior To Shifts
According to OSHA, all forklifts must be inspected daily before they are put into use. If the forklifts are used 24 hours a day, you’ll need to investigate after every shift.
The operator must do a visual inspection with the engine turned off before starting the equipment and then an operational check with the engine running.
Failure to start each shift by checking a forklift and operators are susceptible to equipment damage, property damage, injury and death. A vehicle that is defective or not safe shall be out of service.
Operators must note any equipment problems and immediately report them to a supervisor.
Failure to Wear Seatbelts
Data has proven its effectiveness in injury and mortality prevention. Though seatbelts cannot prevent an accident from happening, they can help keep the individual from sustaining serious injuries.
OSHA forklift safety guidelines state:
“OSHA’s enforcement policy regarding the usage of seatbelts on powered industrial trucks is that employers must require that operators of powered industrial trucks that are equipped with operator restraint devices (e.g., seatbelts) use the devices.”
Make sure you enforce seatbelt compliance for every worker on every shift.
Failure to Regulate Load Capacity, Center and Arrangement
Workers should always be aware of the rated load capacity of a forklift. They also need to know the load center. If the load center is far from the mast, the forklift may become unstable and tip over.
To prevent load-related safety issues, ensure each load is arranged in a safe and stable manner. Center the load as best as possible. Do not overload the equipment.
Failure to Ensure Visibility
The visibility in warehouses and other job sites is often limited. Remind workers to be slow at corners and intersections. So, some basic safety tips that you should remind your group: Always try to be aware more in the direction that you are going and everything that is around you.
(Workers should always make sure their path is unblocked.) The best way to let people know you’re coming around the corner is to sound your horn as a warning at corners, doorways and entrances.
Adhere to speed limits, maintain a considerable distance from other trucks, and avoid potential hazards by switching on headlights if there is a possibility of working at night or outdoors. Both spotters (if there are any dangerous blind spots) and other apps may be needed in some situations.
Insufficient Verification of Safe Floor and Ground Conditions
One area that plays a significant role in safe forklift operation is surface conditions. Your operating surface needs to be stable enough to support the weight of the forklift, its load and the operator. it should also be free of holes, grease, oil or anything else that could cause the lift truck to skid, bounce or tip over.
if used for outside, conditions such as potholes, mud, gravel, ice, snow and soft soil may stuck the forklift or hinder the break process.
Within a plant or warehouse, clutter like loose paper, dust, water or oil on the floor can also create issues with braking. Ensure that the floors are always clean and dry.
Takeaway
Safety starts at the top.
If your employees observe their managers cutting corners on safety regulations, they will cut corners on them as well. Clean up your approach to downsizing: Ensure your staff understands there will be no reprimands for reporting safety hazards that may cause downtime.
These safety procedures will only be useful if your entire team is on alert. The importance of instructing your employees to keep an eye on potential workplace hazards themselves cannot be overstated, either.
Regular training while on the job and inspections, in addition to operational safety protocols will keep your people safe.
Try asking the “Five W’s”:
- Who? Who exactly will be operating the forklift and is he or she trained and certified?
- What? is it aligned, what is the load capacity?
- Where? Where will the work be conducted, and how is the terrain and visibility?
- When? Last inspection date with OSHA standards compliance.
- Why? Why does this operator match up best for the job?
We Can Help!
Our Forklift Safety Training Course at Safety Counselling provides the training, resources, support, and guidance to keep workers safe and to promote a productive work environment. For all your safety training needs contact us.
Schedule Forklift Safety Training today!