Rough Terrain Forklift Training is Paramount to Worker & Job Site Safety – Here’s Why
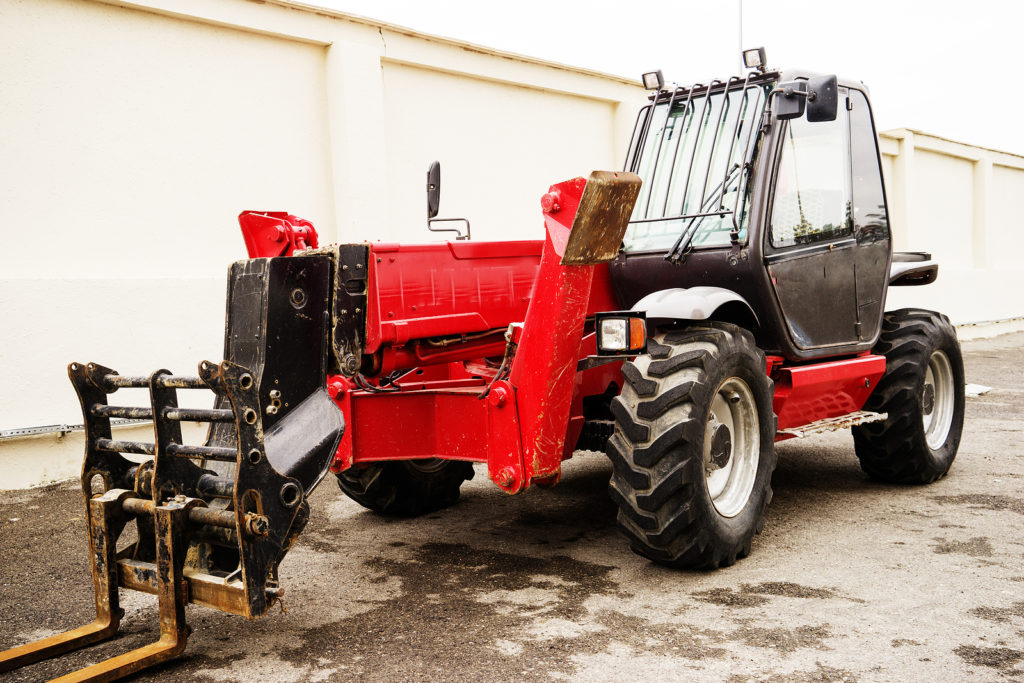
Operating a forklift seems easy, right? Just drive up, lift some stuff, drive away. Piece of cake! However, looks can be deceiving. All forklifts are not created equal, and each type requires specific training to operate safely.
This is especially true for rough terrain forklifts. These heavy machines are designed for the challenges of outdoor jobsites with uneven terrain. Without proper training, they can easily tip over, endangering the operator and others nearby.
What Makes Rough Terrain Forklifts Different?
Rough terrain forklifts, sometimes called all-terrain forklifts, are built for outdoor use on loose dirt, gravel, mud or other uneven surfaces. They have a few key differences from standard warehouse forklifts:
- Bigger tires with deep treads for traction on mud and rocks. These monsters can be up to 5 feet tall!
- All-wheel steering that allows tighter turns for maneuvering around obstacles. The rear wheels turn opposite the front wheels.
- High ground clearance so they can drive over bumps, holes and debris. Some models lift up to 36 inches off the ground.
- More stability features like wider wheelbases and low centers of gravity to handle shifts in weight.
These design tweaks allow rough terrain forklifts to tackle tough outdoor jobs that warehouse forklifts just can’t handle. But they also make the machines harder to operate safely.
The Risks of Untrained Operators
It’s tempting for employers to think: “Joe’s been driving forklifts for years, so he can handle this monster no problem.” While experience is valuable, driving a rough terrain lift is a totally different ballgame. Without proper training, Joe and his coworkers face serious risks including:
- Tip-overs. This is the #1 cause of forklift fatalities. The uneven ground and shifting loads found on constructions sites make rough terrain lifts especially prone to tipping.
- Falls. Lifts designed for indoor use have enclosed platforms to prevent falls. Rough terrain models are open and require caution near ledges or drop-offs.
- Collisions. Bigger blind spots combined with limited visibility on job sites lead to collisions with objects or other vehicles. Proper spotting techniques are essential.
- Load handling errors. Outdoor loads like pipes or lumber shift uniquely and need special handling techniques. Improper moves can damage materials or crane the operator’s neck.
- Unfamiliar controls. Control levers, pedals and steering wheels vary widely between forklift types. It takes training to know how each machine handles.
Sadly, lack of training leads to dozens of rough terrain lift deaths and thousands of injuries each year. But proper instruction can prevent these needless tragedies.
Required Training for Safe Operation
The good news is specialized training for rough terrain forklifts is now required by OSHA. Employers must train operators and certify their skills before turning them loose on one of these massive machines. Proper instruction covers:
- Load capacity & stability. Understanding how to avoid overloads and maintain stability on uneven ground.
- Refueling & maintenance. Learning safe procedures for fueling, battery changing and routine care.
- Safety devices. Proper use of seat belts, load back rests, lift locks and other safety mechanisms.
- Surface evaluation. Techniques for assessing ground conditions before lifting or traveling.
- Load handling. Specialized moves like boom and jib operation for unique loads.
- Traffic safety. Following site rules of the road for smooth coordination with other vehicles.
- Operator fitness. Ensuring operators are not impaired by fatigue, illness or substances that reduce alertness.
Completing OSHA’s required training program ensures operators are fully prepared for the unique demands of rough terrain forklifts. Certification testing validates their mastery of safety skills.
Continuing Education for Changing Conditions
Initial training is vital, but maintaining skills is also key. Regular refresher courses help operators remain alert to hazards. Job sites change rapidly, bringing new challenges like:
- New equipment & attachments. Forklifts may use new attachments like booms for special lifts.
- Different materials. Unfamiliar loads like drywall or barricades change balance and visibility.
- Weather factors. Rain or snow transforms terrain and requires adjusted techniques.
- Site layout. Buildings go up, ditches get dug – the landscape continually evolves.
- Fatigue. Long shifts or schedule changes can impair judgement and focus.
Refreshers prepare operators by rehearsing safety skills in new simulated environments. They also provide a forum to discuss concerns and lessons learned on the job.
Shared Responsibility for a Culture of Safety
While training sets the foundation, safety must be a team effort. Everyone on site shares responsibility including:
Operators who follow their extensive training to the letter during every shift. They stay focused, alert and committed to safe procedures.
Managers who schedule sufficient training, encourage open discussion of hazards and lead by example. They also ensure equipment is properly maintained.
Coworkers who watch out for each other and speak up about any safety concerns they notice. They know calling out issues helps keep the team protected.
Engineers & architects who design job sites with forklift safety in mind. They allow adequate operating space, tested lift surfaces and highly visible markings.
When all levels work together to prioritize safety, the job site becomes an environment where operators can put their specialized training into safe practice.
Stay Alive with Rough Terrain Forklift Safety
Operating rough terrain forklifts involves serious risks, but also incredible rewards. These powerful machines allow construction projects to succeed on any terrain.
Specialized instruction combined with open communication gives forklift crews the knowledge and skills to navigate any landscape. Stay safe out there!